
How to measure tactile pressure: Easy and Precise Pressure Profile Visualization
Keywords: Printed circuit board manufacturing, quality assurance in electronics, lcd glass substrate circuit formation Fuji Prescale Film Summary: Manufacturing of PCBs and LCD glass substrate circuit formation requires precise and constant pressure on the entire working surface. Fuji Prescale enables easy and reliable way to measure pressure distribution and thus ensures high quality and productivity. Written by Igor MateskiLamination in PCB and LCD Manufacturing: Challenges and Problems
Manufacturing printed circuit boards and lcd panels on industrial scale poses quality assurance challenges, and is accompanied with various problems due to surface material consistency.
In some cases, when the pcb leads are transferred onto the board, the lamination process gets distorted due to pressure irregularities along the width and/or length of the lamination roller. These pressure irregularities cause the dry film to wrinkle. Sometimes, even bubbles get trapped in the pcb due to surface irregularities.
Wrinkling and bubbles cause various defects in the leads quality, which results in defective products, or worse, numerous warranty claims when the electronic device gets out on the market and fails as a result of poor pcb wiring quality.
How Manufacturers Usually Deal with Manufacturing Defects
To ensure reliability and quality, manufacturers rely on Quality Assurance of each batch. This process is checking for manufacturing irregularities in retrospect, so if and when a defect is discovered, the entire batch between checks is with questionable quality.
Usually, when the defect is discovered, repairing the pcb lamination machine requires a trained technician that is sent out by the machine manufacturer. This takes plenty of time, creates unwanted expenses, and during the down time the manufacturing schedule needs to be adjusted.
The usual repair process is basically a trial and error method of eliminating suspects:- Is the roller surface transferring pressure evenly along the length?
- Is the roller axis still in line with factory specs or the roller wobbles?
- Is there a detectable planar axial distortion that causes wrinkling and skewing of the dry film?
These defect scenarios take time to detect and repair, and during all this time manufacturing is on hold.
Two-step Way to Identify Manufacturing Defect with Fuji Prescale
The three listed defect scenarios can easily be checked using the Fuji Prescale LLLW or LLW grade film. It only takes two checks to establish a precise diagnosis of the defective lamination machine.
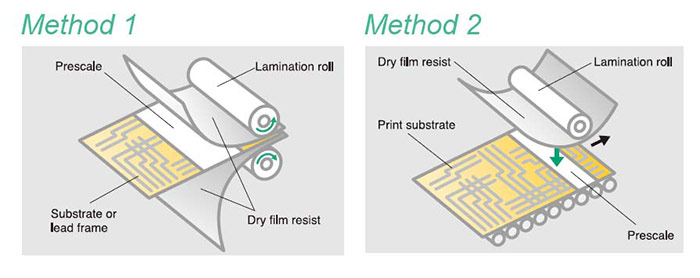
The first detection method relies on testing surface consistency along one rolling length of the lamination roll. This first step reveals any vertical axis distortions, as well as surface irregularities of the lamination roll.
The second testing method reveals only axial alignment and pressure distribution along the length of the roller. In this case, the prescale film is only placed between the lamination roll and print substrate, and the roll(s) are applied onto the board with nominal pressure.
The image below shows the results of the two-step testing.
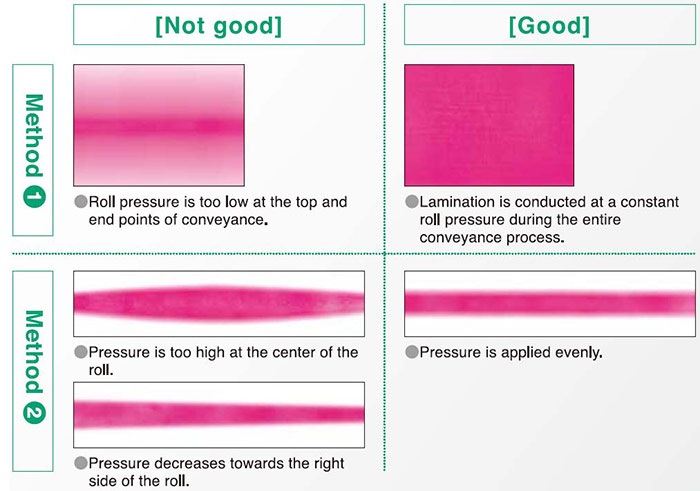
With Method 1, the roll pressure can be low at one rotating length, and higher at another. This means that the roller bearings are defective or the roller surface is defective. If the developed Fuji Prescale film is evenly loaded with pressure, as it is on the image in the upper right corner, then manufacturing can resume.
With Method 2, several axial defects can be detected.
The first image shows a developed Fuji Prescale where there is bulging caused by an excessive pressure load at the center of the roller. This may be caused either by roller surface damage, or even a roller axis damage.
The second image shows yet another axial defect, where the developed Fuji Prescale film shows a cone-shaped pressure distribution. This defect is characteristic of a defect where one end of the roller axis transfers heavier load than the other end of the axis.
If the developed Fuji Prescale is identical to the image to the right, then the roller axis is properly aligned and manufacturing can resume.
This case study clearly shows that with Fuji Prescale, PCB and LCD manufacturers can greatly benefit:- Fuji Prescale saves time in detecting manufacturing problems
- Thanks to Fuji Prescale films, repair technicians can do preventive testing before defects arrive
- Manufacturing can quickly be restored thanks to fast repair procedures