Measuring Pressure Distribution Of Solder Cream Application for Surface-Mount Devices
Keywords: SMD component soldering, ensure proper solder conductivity, squeegee pressure, proper solder cream distribution, measuring substrate pressureSummary: Surface-Mount Devices (SMDs) need just the right amount of solder cream on the PCB pads to ensure adhesion of the SMDs and subsequent proper conductivity after the PCBs go through a soldering machine. Measuring if the solder cream is applied with the nominal pressure is crucial, and the only practical and reliable way is to use the Fuji Prescale film.
Written by Igor Mateski
Solder Cream Distribution Mechanism
In mounting SMD components such as diodes, capacitors, resistors, ICs etc, each PCB pad needs a specific amount of solder cream to ensure proper positioning and conductivity of the soldered junction. The process of applying solder cream relies on perforated Mask and a squeegee that pushes the solder cream through the mask onto the corresponding PCB pads, as shown on the image below:
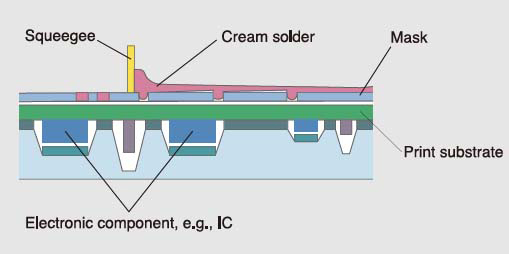
The squeegee mechanism of applying solder cream onto the PCB pads relies on uniform nominal pressure throughout the width and length of the print substrate so that the solder cream can penetrate the perforated mask and land on the PCB pads.
Manufacturing Challenges of Solder Cream Application
The problem arises when on some pads there is more cream than needed, while on others there is barely any solder cream present. These inconsistencies will affect the quality of each of the solder joints and depending on the fault tolerance built into the design, the final electronic product will either work unreliably, or not work at all. Manufacturers need a reliable production line that can make high-quality PCBs with all components properly soldered, each and every time. Since the mechanism of applying solder cream onto the PCB pads is through perforated masks, ultimately the physics behind this process is that of viscous fluid flow through a small nozzle. Since the viscosity is constant, what defines the amount of fluid flow is the surface area of the nozzle (i.e the size of each PCB pad), and the pressure exerted by the squeegee. As the surface area of PCB pads varies from component to component and is not ultimately a manufacturing variable, the only component that influences manufacturing quality is the pressure the squeegee exerts onto the substrate. So for manufacturers to ensure proper solder cream application onto the substrate, they only need to make sure that the squeegee exerts constant pressure along the entire substrate surface. However, there are almost no reliable ways to measure this pressure.
Benefits of Measuring Nominal Pressure with Fuji Prescale
The Fuji Prescale LLLW Ultra-Low Pressure and the 4LW Extremely Low Pressure films are the only reliable method of reading out the pressure exerted onto the substrate. Technicians can use it on-the-spot and run regular maintenance tests to make sure the squeegee does its job properly. All a technician needs to do is cut the Fuji Prescale to-size and place it between the substrate and mask, as shown on the image below:
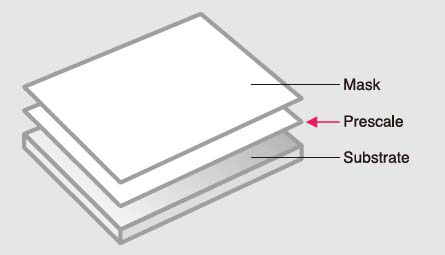
Once the Fuji Prescale film is placed properly, the squeegee needs to apply solder cream as usually, and the pressure exerted through the solder cream develops the Fuji Prescale film. Then the technician can run a visual inspection for any pattern inconsistencies or scan the developed Fuji Prescale film and read out pressure values. The image below shows two developed Fuji Prescale films:
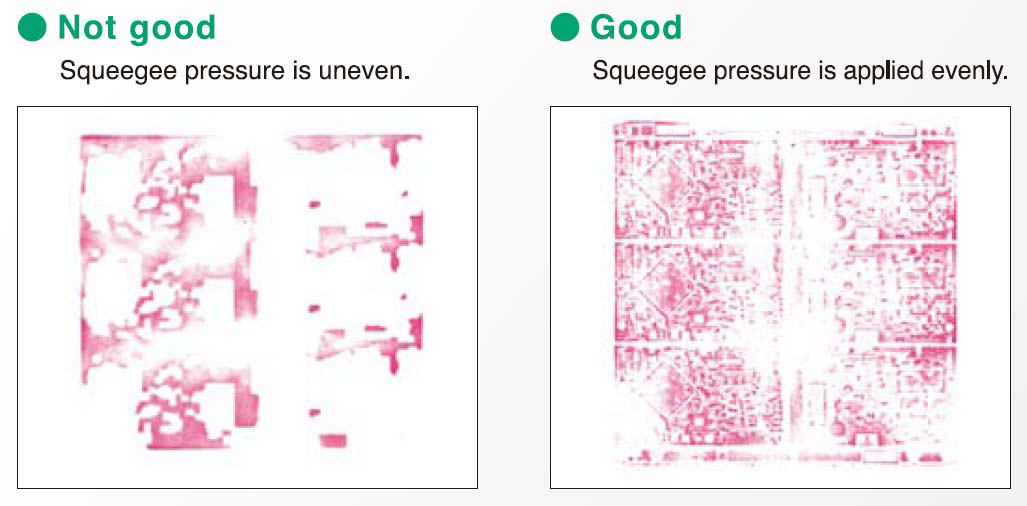
The image on the left is from a defective squeegee and it is quite obvious that there are large areas where the pressure is not sufficient to push the solder cream through the perforated mask and onto the PCB pads. The image on the right is from a proper solder cream application machine where the squeegee evenly distributes the solder cream onto all PCB pads of the substrate. Using the Fuji Prescale to determine the quality of solder cream application has several advantages:
- Direct measurements of the distribution pressure
- Fast measuring procedure with very little down time in production
- Cheap solution that allows for regular maintenance checkups to ensure high production quality