Mapping Tactile Pressure in Laminated Battery Structures
Written by Igor Mateski
Keywords: tactile pressure, lamination pressure, bolted joints pressure, supercapacitor manufacturing, measure tactile pressure, pressure gauge
Summary: Green energy requires reliable energy storing systems. Supercapacitors are great storing devices that rely on even tactile pressure to store the maximum amount of energy packed in a smallest possible dimensions. Using the Fuji Prescale film, engineers have a direct way of gauging capacitance consistency based on tactile pressure readouts.
Supercapacitors as The Batteries of the Future
In the past couple of decades the issue of green energy intensified drastically. The largest economical breakthroughs of green energy sources are solar and wind power. As both these energy sources are cyclical, the critical question is not what sources to utilize for green energy, but how to sore the produced energy during peak hours and use it during down periods.
Energy storing technology is now also catching up and there are already commercially available high-power, high-capacity storage devices. Also known as EDLC or supercapacitors, these electrochemical double-layer capacitors are closer in utility to standard Li-Ion batteries than capacitors, with a difference of EDLCs having much higher energy storing capacity.
Unlike regular capacitors that have two plates, a positive and a negative, these double-layer capacitors have ion permeable layers in between that allow for much higher capacity density without increasing surface area or materials:
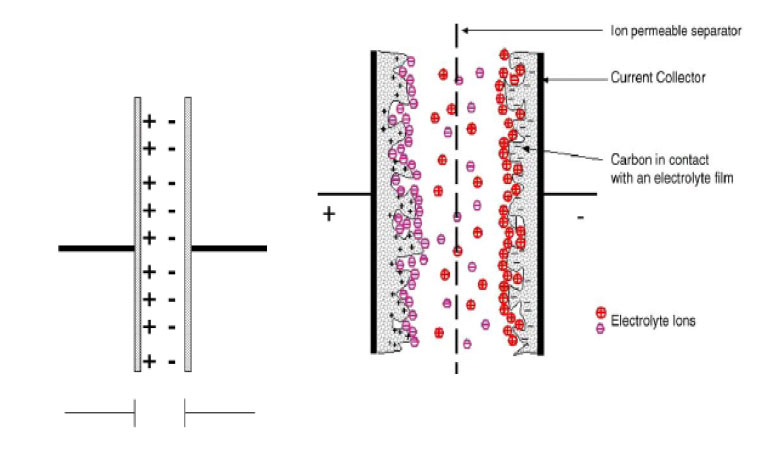
Bolted joints tactile pressure affects power efficiency
Increasing Power Density
From electrochemical laws, the easiest way of increasing energy density is by increasing voltage of the stored energy. Other ways of increasing the storage capacity is by increasing the surface area, using more conductive electrolytes and reducing the distance between plates.
This last variable, distance between plates, is where our focus lays. From a manufacturing perspective, capacitors, as well as supercapacitors, are laminated devices. Stacking of the plates and electrolytes is a lamination process and is subject to issues like tactile pressure in relation to plate surface, so supercapacitors researchers opt for smaller size of electrodes, and uniform tactile pressure to achieve higher capacitance. Below is an image of such laboratory version of a supercapacitor:
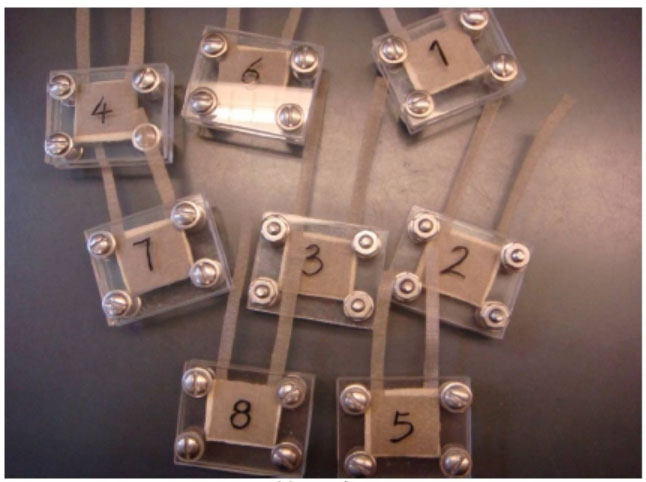
Bolted joints tactile pressure affects power efficiency
These lab speciments, hand-made superconductors rely on a bolted joints design to ensure proper tactile pressure between the electrodes. Tightly packed laminated assemblies account for packing more storage capacity in a smaller-sized supercapacitor batteries.
Tactile Pressure as Capacity Uniformity Gauge
Increasing capacitance while keeping voltage and materials expenses down is the key focus of manufacturers. This is why engineers and lab technicians use the Fuji Prescale film to acurately measure the needed tactile pressure and how it affects capacity of manufactured versions of supercapacitors.
Depending on the needed capacity and electrolytes used, lab technicians need to create the lab versions of these superconductors with a nominal surface pressure.
The easiest way to directly measure tactile pressure is to use the Fuji Prescale film from the pressure range that matches the calculated value. The image below is a sample lab-made supercapacitor
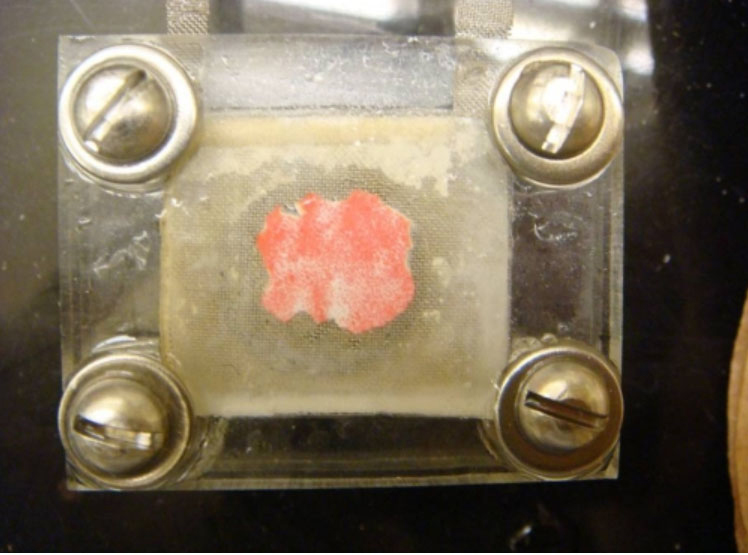
Surface roughness causes power losses
Technicians can easily read out the pressure distribution along the tactile surface by simply recognizing patterns of red pigmentation.
In this particular case the electrolyte-electrodes lamination seems to be experiencing uniform tactile pressure so technicians can be sure that the capacity variation will be minimal.
Thanks to using the Fuji Prescale film, engineers and technicians can establish a visual cue of how the capacitance varies. With even tactile pressure supercapacitors can be manufactured on large scale with minimal capacitance losses due to tactile pressure inconsistencies.
But as surface roughness and machining processes create areas of uneven, out-of-flatness areas, the pressure distribution must be measured in order to precisely establish a proper tactile pressure every time. Inversely, measuring and visualizing these surface imperfections can create a map of the resistance and heat generating areas, as both resistance and heat are directly dependant on the tactile pressure.
Below are actual screenshots of surface roughness measurements and a developed Fuji Prescale film revealing the out-of-flatness areas which in turn are the areas of highest resistance and highest heat:
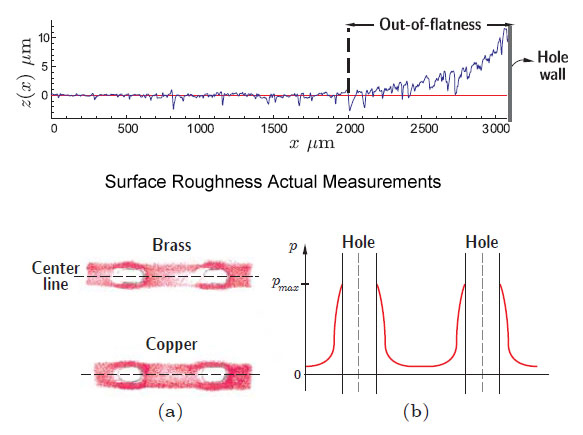
Fuji Prescale Pressure Mapping on Bolted Electrode Brackets
In both measurements, the out-of-flatness areas account for increased tactile pressure. These areas are due to the punctuating of the mounting holes, usually done by stamping.
In this particular case two different materials were used (Copper and Brass), and as the Fuji Prescale film snapshots reveal, Copper turned out to be a better material for using brackets because of its better surface roughness profile after stamping.
Thanks to using the Fuji Prescale film to get actual tactile pressure mapping, engineers can design Li-Ion battery assemblies that will not be as prone to power loss.
Related Case Studies for Lamination Pressure and Roller Defects :
Visualization and Measuring Tactile Pressure using Fuji Prescale and FDP 8010 Digital SystemUsing Fuji Prescale as Quality Assurance in Fuel Cell Manufacturing
Using Fuji Prescale As Comparative Measurement of Thermal Conductivity Between Aluminum Plates