Increasing Quality and Quantity of LCD Panel Manufacturing With Using Fuji Prescale Film
Keywords: LCD manufacturing, quality control during lcd manufacturing, detecting defects of polishing equipment Summary: LCD Manufacturing is an ever-growing industrial segment with big demands on quality and quantity. Manufacturers can greatly benefit from the Ultra-Low Pressure Fuji Prescale Film as a means of Quality Assurance and increased manufacturing yield. Written by Igor MateskiThe Growing Need of LCD Panels
With the ever-increasing number of LCD devices, the market needs also increase. There are over 5 billion cell phones in use world-wide. Add to it the number of laptops, LCD TVs, Sat-Navs, smart cars etc. and it would not be an overstatement to say that there's at least two LCD panels per each person on Earth, and it keeps on growing.
LCD manufacturers are pressed to launch new LCD panel models with higher resolution, higher contrast, lighter, tougher, touch-sensitive, multi-touch sensitive, cheaper, more reliable... the list goes on.
LCD Screens and Tactile Pressure
In order for LCD manufacturers to keep track with the growing demand for high-quality LCD panels, there is a constant pursuit of improving the manufacturing process.
One of the key LCD panel requirements is ideally flat surface so that contrast and color-consistency are as high as possible. To achieve this, manufacturers rely on precision polishing machines that use even tactile pressure and polishing solvents to achieve high-grade panel shine for each individual LCD panel.
The polishing process relies on close to perfect vertical alignment of the polishing head, stage and LCD panel itself. Small discrepancies of this alignment will result in un-even pressure distribution that can lead to surface chipping of glass shavings. When the polarizing plate is mounted to a panel with glass shavings, the quality of the LCD assembly will be compromised because of the trapped air bubbles around these glass shavings.
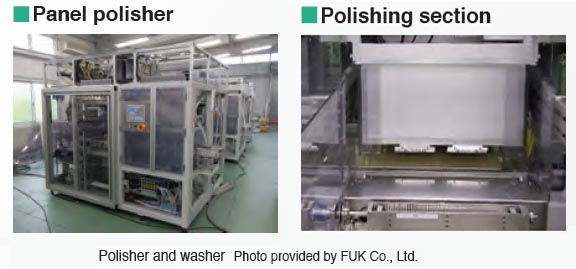
How Fuji Prescale Helps Manufacturers
Glass shavings and air bubbles are common problems for LCD manufacturers.
Even though the washing of the polished surface may help, in reality this is only treating the symptom, not the underlining cause for it. Uneven pressure distribution is what causes the glass shavings, and solving the alignment problem is best done using the Ultra-Low Pressure Fuji Prescale Film.
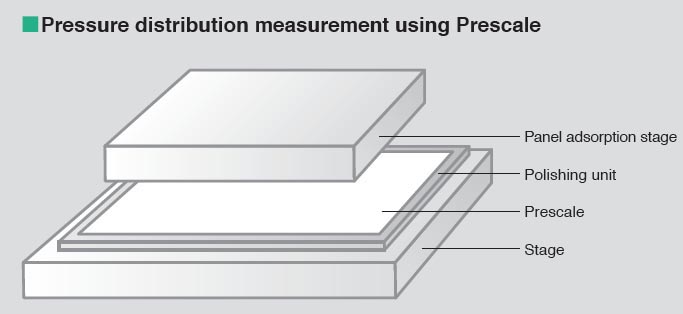
The illustration above shows how the Fuji Prescale film can be used.
The Prescale film is placed between the polishing unit and the panel adsorption stage and the nominal pressure is applied. This develops the Fuji Prescale film and the read-outs can be used to directly determine the plate alignment.
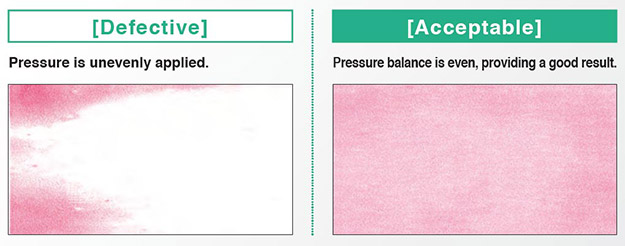
The image above is a sample developed film of a defective and acceptable plate alignment for an LCD polishing machine.
The image on the left is from a defective polishing machine where the plates are not in alignment. The tactile pressure is out of balance to such extent that there is barely any pressure exerted on almost 2/3 of the tactile surface. Such misalignment will cause chipping and air bubbles will be an inevitable result.
The image on the right is from a evenly balanced tactile pressure along the contacting surface, which will produce solid LCD polished surfaces.
Using the Fuji Prescale film, the LCD manufacturers can increase overal quality and yield by quickly and easily testing polishing machines for alignment. Thanks to the Fuji Prescale film's on-the-spot readouts, technicians can run maintenance checks often and ensure a consistent manufacturing quality. This will in turn result in reliable products and optimally utilized manufacturing time.