Fuji Prescale LLW Pressure Mapping as Vertical Alignment Gauge In Nanoimprint Lithography Manufacturing
Keywords: nanoimprint lithography, Fuji Prescale LLW, vertical alignment measurement, pressure mapping, digital pressure mapping system
Summary: Nanoimprint Lithography enables fast manufacturing but needs regular vertical alignment checks to ensure quality. The Fuji Prescale Film enables fast, easy and straightforward vertical alignment evaluation by mapping the tactile pressure between the substrate and mold carrier.
Source: Harutaka Mekaru, Ultrasonic Nanoimprint on Poly(ethylene terephthalate) at Room Temperature, Japanese Journal of Applied Physics Vol. 47, No. 6, 2008, pp. 5178-5184
Written by Igor Mateski
The Technical and Economic Challenges Nanoimprint Lithography
Nano Imprint Lithography (NIL) is used for manufacturing DVDs. Current manufacturing processes are limited by the plastic material used (PET) and time of temperature-exposure for proper formation. So for each CD/DVD it takes 2 seconds of exposure on temperature for a proper litographic imprint. Cutting the exposure time will effectively increase manufacturing output and lower the price per item. One option is to lower the need of high temperatures so the operating temperature is reached faster. However, piezoelectric ultrasonic actuators cannot exert pressure forces that would ensure proper imprints. This is why a temperature of 180 degrees centigrade is used, and a 2 seconds exposure ensures proper imprint.
The other one is dealing away with temperature and perform imprints on room temperatures. An experimental ultrasonic NIL actuator replaced the standard piezoelectric with magnetostriction actuator, enabling higher ultrasonic vibration and eliminating the need of heat completely. Thanks to friction-induced heat (measured 100 degrees raise in only 1 second of ultrasonic vibration), ultrasonic lithography can be performed without need of external heat. This experimental imprint machine combines the effects of high-speed press and frictional heating of plastic.
The Problem of Vertical Alignment Consistency
Performing proper lithography on a massive scale used in manufacturing plants is a daunting task. With piezo-actuators the ultrasonic vibrations are not as strong so vibration-caused alignment discrepancies are not as big of a problem. However, with the suggested cold ultrasonic lithography using magnetostriction actuators, the scale of vibration is on a completely different scale. This means that vibration-induced alignment problems grow significantly. Alignment issues grow in importance as the suggested cold lithography machines have other alterations, as shown on the image below:
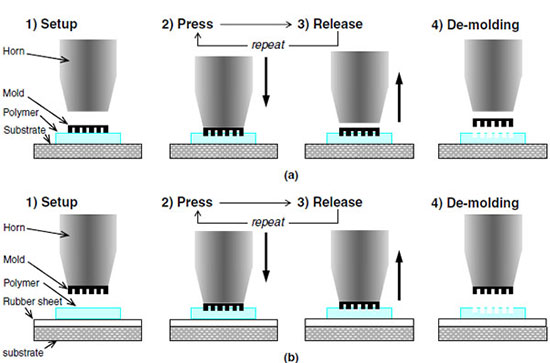
The image above illustrates warm (Detail a) and cold (Detail b) lithography processes. The warm, standard piezo-actuator lithography exerts only downward force, while in the cold process the horn holds the mold and exerts upward and downward movement so any vertical misalignments cause double trouble, causing deformations of ridges.
Using Fuji Prescale to Reliably Map Tactile Pressure
Micrometers that align the lithography head (horn) cannot reliably preserve alignment for longer periods of time because of the nature of ultrasonic lithography. The forces exerted onto the substrate also apply onto the micrometers alignment structure and ultrasonic vibration inevitably misaligns the entire print head. This is why running regular alignment checks is extremely important for ensuring high lithography quality.
By using the Fuji Prescale LLW film placed between the Aluminum mold and bottom loading stage technicians and engineers can reliably measure pressure distribution throughout the contact area and make needed adjustments using the micrometers alignment mechanism of the print head. These measurements and alignments are done without a PET substrate, when the Aluminum mold carrier is machined to size, as shown on the image below:
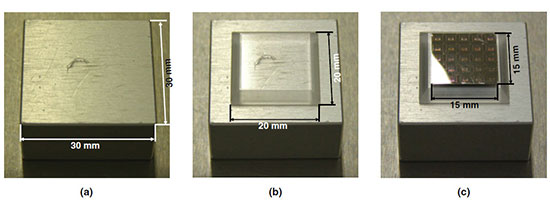
The Aluminum mold carrier starts off as a block measuring 30x30 mm. (Detail a). Then it is machined to fit the needed mold dimensions (Detail b), and finally the mold itself is attached (Detail c).
Mapping the tactile pressure is done after machining the block, so that the pressure is measured only on the surface of interest. The image below shows how the measurement is done:
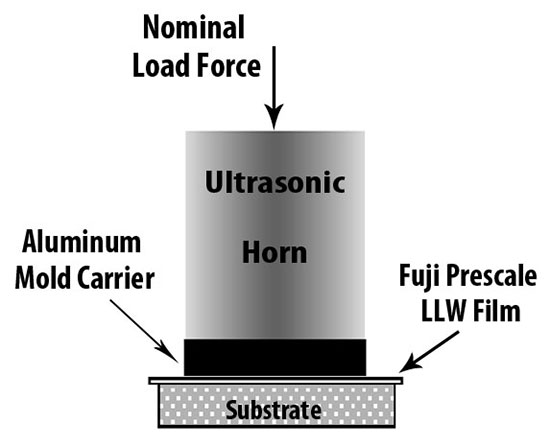
As the illustration above shows, the Fuji Prescale LLW Film was used to map the tactile pressure between the aluminum mold carrier and the substrate. The LLW Prescale Film is cut to size, placed on the substrate plate, and then the nominal load force is applied onto the stamping head (aka. ultrasonic horn). This load force develops the Prescale Film and technicians can visually inspect the pressure map and establish a diagnosis of the alignment between the substrate and the mold carrier.
Below are screenshots of developed Fuji Prescale LLW Films that showcase a misaligned mold carrier (detail on the left) and a properly aligned mold (detail on the right):
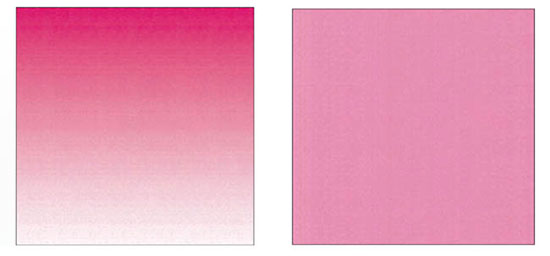
As the pressure map on the left reveals, the Aluminum Mold Carrier is misaligned. Thanks to this visual cue technicians can immediately adjust the alignment using micrometers attached to the print head. After alignment, the mold carrier is perfectly aligned with the substrate, as the developed Fuji Prescale Film shows. There is no need of digitizing the films in order to perform proper alignment, but engineers can use the Fuji Prescale Distribution Mapping System to keep records of misalignments and compare them over time to establish a more elaborate theory as to why misalignments happen and if they eventually would need to replace some of the micrometers and tightening mechanisms of the ultrasonic horn.
Thanks to the ease of use of the Fuji Prescale LLW Film, the visualization of tactile pressure and fast pressure mapping engineers and technicians can quickly, cheaply and effectively eliminate any alignment problems and resume manufacturing sooner than with any other diagnostic procedure. Using the Fuji Prescale Film as a diagnostic tool saves manufacturing time and eliminates the danger of losing entire batches of poorly manufactured items.