Ensure High Quality Adhering of AR, AG, OCA Functional Films to LCD Screens Using Fuji Prescale
Keywords: Ensure perfect adherence of anti-glare (AG) films to LCD, adhere anti-reflex (AR) films to LCD, using optically clear adhesive (OCA) in touchscreen manufacturing, diagnosis of functional film adherence, fuji prescale tests in functional film adherenceSummary: Adhering functional films to LCD screens such as anti-glare (AG), anti-reflex (AR) as well as usingĀ optically clear adhesive (OCA) in touchscreens requires uniform pressure to avoid air bubbles, flexing, skewing and other film displacements. Using the Fuji Prescale Ultra-Low Pressure film helps in diagnosing and eliminating any adherence problems.
Written by Igor Mateski
AR, AG, OCA Functional Films and LCD Usage
With the explosive spread of LCD devices on the market, companies look for ways to make their product better in any possible way. For this reason, manufacturers add various functional films to various LCD devices:
- smartphones
- PDAs
- iPad and alike
- laptop screens etc.
Improving visibility and durability of LCD screens involves adhering of Anti-Reflex (AR) films, Anti-Glare (AG) films. Producing touchscreen devices requires using optically clear adhesives to add the resistance or capacitive touch-sensitive films. All these functional films must be flawlessly joined with the base plate to ensure optimal visibility of the displayed information on the LCD.
Challenges in Adhering AR, AG, OCA Films to LCDs
The method of adhering functional films to the base plate uses rollers that must exert equal pressure throughout the contacting surface so that the functional film is evenly adhered onto the plate. However, in practice, ensuring even pressure is not easy. The larger the adhering surface, the larger the problems.
In some cases, the roller axis can deviate from its ideal perpendicular aligmnent to the plate's movement vector. This can cause the functional layer to get skewed or wrinkled.
Also, if the roler axis is not ideally parallel to the base plate, the roller will exert more pressure on one end, and lesser adhesion pressure on the other side of the base plate. This can cause air bubbles or poor adhesion of the functional screen.
Benefits of using Fuji Prescale in the Adhering Phase
In order to avoid any imperfections during the manufacturing process, technicians must regularly monitor the roller-cover glass alignment to ensure proper adhesion of the functional films.
The best way to measure alignment is to measure the tactile pressure that the drum exerts on the cover glass using the Fuji Prescale Ultra Low Pressure (LLLW) prescale film, as shown on the illustration below:
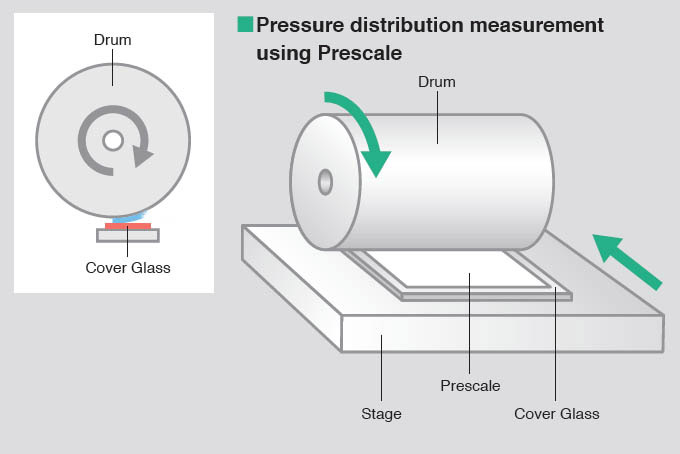
The Fuji Prescale film is placed between the cover glass and roller. The roller then rotates to cover the entire surface of the cover glass. This will develop the Fuji Prescale film which then can offer easy and accurate visual inspection, or it can be fed into the FPD-8010E Pressure Mapping System for precise pressure measurement and visualization.
Below is an image of actual test results of a defective and acceptable roller alignment:
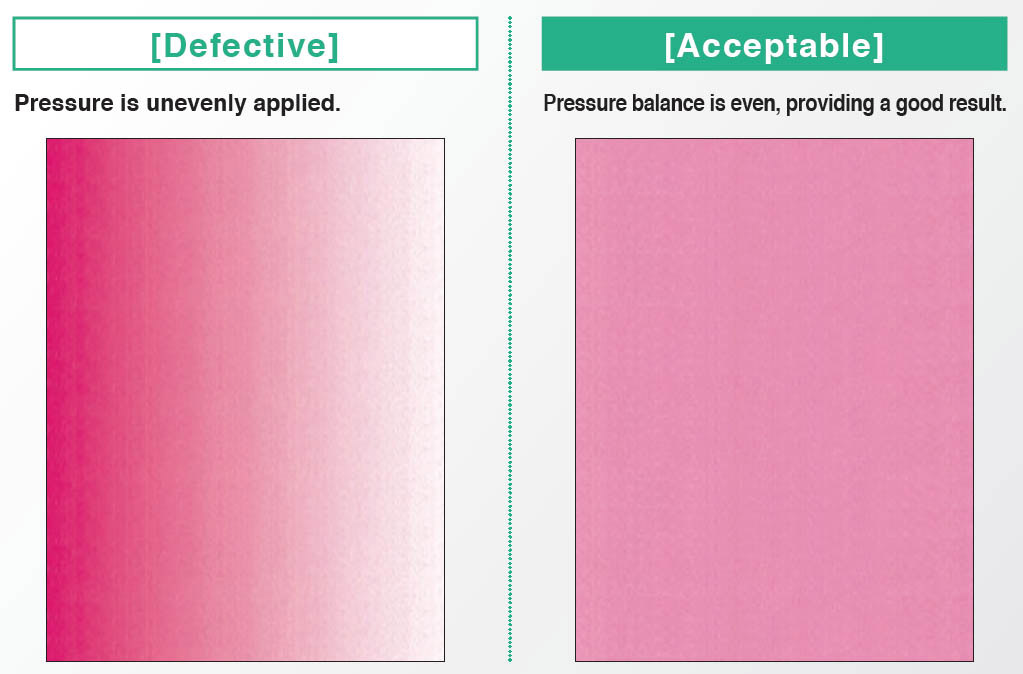
In this case, the roller was not exerting the nominal pressure throughout the surface. Although the pressure was enough to achieve adhesion of the functional layer, the lack of binding pressure resulted in poor adhesion of the functional layer. This defect will only be discovered during the lifetime of the product, which can result in material loss due to warranty claims.
Thanks to the timely usage of the Fuji Prescale film, this manufacturer ensures optimal production quality of the LCD assembly as well as standardized LCD quality throughout the manufactured volume.
The Fuji Prescale Film is the only way to do pressure gauging on-the-fly, without expensive tiral and error procedures.