Designing Head-Gasket Bolted Joints with Fuji Prescale and FEA
Written by Igor MateskiKeywords: bolted joints design, combustion engine design, head-gasket tactile pressure, thermo-mechanical bolted joints design, fuji prescale
Summary: Engine design inevitably revolves around designing the bolted joint of the thermo-mechanical head-gasket-body assembly. Moving away from experimental to computational design speeds design but engineers must use Fuji Prescale to verify computational findings and further improve the bolted joint design.
Engine Bolted Joints Challenges
Rapid prototyping pushes engineers to use approximations in engine design which inevitably leads to speed up designing the crucial head-gasket-body bolted joint assembly.
Since this assembly is thermo-mechanical in nature, proper elements design and establishing the nominal tightening force further complicates matters. Engineers are pressed to pull out the maximum power while reducing engine weight so over-dimensioning of bolted joints to improve safety factors is not an option.
The only reliable way to design bolted joints is to submit the entire engine to dynamometer testing which is a lengthy and expensive process with numerous prototype updates.
Designing Bolted Joints with FEA
To achieve fast product development without the expansive dynamometer testing engineers use Finite Element Analysis whenever possible.
However, the problem with FEA is that bolts, gaskets and joint elements are simplified in order to make the modeling and analysis time shorter. This in turn poses other challenges. Research shows that when simplifying bolts to cylinders with nominal diameter results in data skewing, and axial tension differs from measured tension by up to 20%. These value variations caused by simplification of elements make the entire FEA process inherently unreliable. Tension values directly influence the tactile pressure and therefore the sealing properties of gaskets in the head-body assemblies. This is why often times FEA results are inconclusive, and although FEA speeds up development, engineers will eventually have to run dynamometer testing to confirm their FEA values with real-life testing.
Fuji Prescale as FEA Refining Tool
There are recent research papers that point out how engineers fine-tuned the FEA process by using the Fuji Prescale film. S.-S. Cho et al. published a short analysis and reporting paper in the International Journal of Automotive Technology, Vol. 11, No. 1, where he describes the process of using a different bolts simplification approach that solves the 20% tension discrepancy thanks to feeding back data from Fuji Prescale measurements.
As Cho states, engineers can run FEA using a new bolt simplification model that results in very reliable force values that correspond to the Fuji Prescale readouts.
The image below is a screenshot of comparing the Fuji Prescale readouts for the tactile pressure of the thermo-mechanical bolted joint, and a FEA rendering of tactile pressure that is applied at the tactile surface between the gasket and engine head. The top section is from an analysis of the peripheral areas of interest such as oil and coolant channels, while the bottom section is a comparison of pressure visualization of the cylinders area.
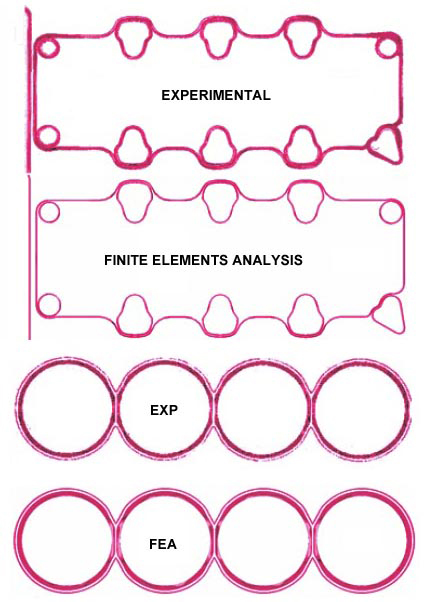
Below is a zoomed detail from the pressure visualization using the Fuji Prescale experimental readout, and an improved FEA approach.
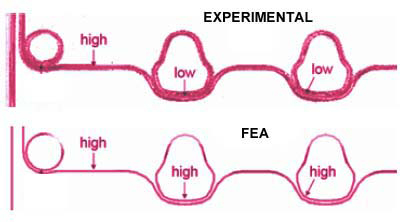
The image above is a good example of why using the Fuji Prescale film is still an invaluable method of tactile pressure visualization.
The experimental pressure readout around the fluid ducts shows that there is a relatively lower tactile pressure which can lead to sealing problems even if the pre-tensioned bolts create areas of nominal high pressure. In comparison, the FEA tactile pressure readouts that are based on approximation report a nominal high tactile pressure.
To remedy this flaw in the FEA procedure Cho reports of using improved procedures in simplifying a threaded bolt with a matching cylinder in the finite-element model of the engine.
This improved FEA model is a result of using the Fuji Prescale pressure readouts to establish a better finite-elements representation of bolted joints during the FEA of engines.
Thanks to the Fuji Prescale, engineers can ensure proper FEA processes and produce solid engine designs without increasing engine weight to ensure acceptable safety factor of the thermo-mechanical bolted joint assembly.