Designing Bolted Composite Structures Using Fuji Prescale Films
Keywords: composite material clamp-up pressure, composite fatigue, measuring tactile pressure in composite structures, nominal tightening force in composite bolted joints Summary: Composite structures used in the US Navy must be reliable for a specified lifetime. Composite fatigue induced by bolt tightening forces negatively affect the tactile pressure. Using FEA and Fuji Prescale helps in establishing the optimal tightening force, number of bolts and tightening type that ensures minimal pressure variation caused by composite fatigue.
Written by Igor Mateski
Composite Structures in the US Navy
In recent time the US Navy in cooperation with university research teams works on creating new types of materials for use in building the hulls of Navy vessels. These hybrid, composite-metal structures should reduce the magnetic signature of Navy vessels, reduce their weight and consequently increase their speed.
Developing of such hybrid hulls with low magnetic signature requires using of non-magnetic stainless steel in combination with EG/VE composites where the composite-metal junction is established with bolts.
These bolted composite structures must ensure water-tightness between the metal and composite as well as the needed mechanical strength of the hull in order to withstand defined operational loads. The water-tightness is achieved by applying a nominal clamp-up load with a number of bolts tightened with a pre-defined tightening force.
Challenges in Bolted Composite Structures Design
While metal-metal water-tight bolted joints are somewhat straightforward to design, composite materials create a special set of challenges mostly because of the visco-elastic nature of resigns. Namely, a composite panel bolted to a metal base is susceptible to loss of clamp-up load where the rate of load loss is affected by the fiber-mesh structure of the composite, temperature, humidity and time.
Research shows that this load loss is a non-linear function and depending of the type of bolting and type of bolts, composite structures bolting load can deteriorate from 13 up to 50%. Such wide pressure variance as a function of time poses significant challenges for Navy vessels.
Using Fuji Prescale and FEA in Solving the Clamp-up Challenge
Cacesse et al. have conducted studies to establish a reliable system to deal with the clamp-up pressure challenge. Their research methodology relied on different types of bolt types, re-tightening after set periods of material creep, and did measurements using FEA and experimental, Fuji Prescale tactile pressure measurements.
As the use of bolted hybrid connections will mostly be used for removable composite panels, special attention was given to water-tightness between the composite and metal base.
Researchers used three different bolted joint designs to test composite creep and bolting pressure, as shown on the image below:
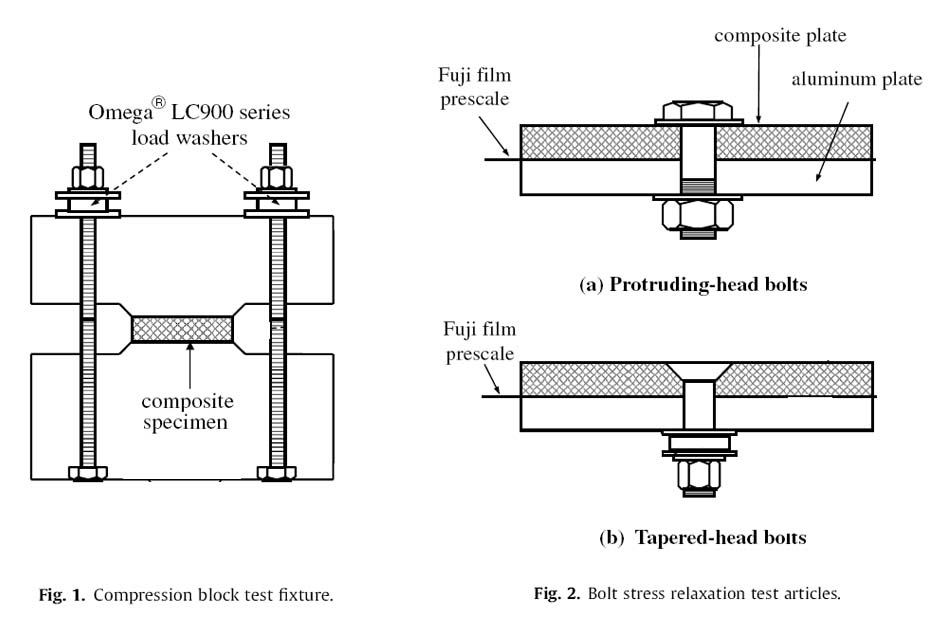
The different testing rigs were intended on revealing the connection between clamp-up load, stress distribution and composite deformations induced by the bolting pressure. The FEA models revealed that with lower initial clamping force, load loss can decay to near zero in a very short period of time. With lower bolt-tightening force, the needed water-tight tactile pressure between the composite and metal plate can be achieved by using more bolts with larger tightening clamp (conclusion derived from Fig. 1, where larger footprint ensured pressure distribution and decrease in composite material fatigue).
Below is a FEA model of how the bolt tightening pressure is distributed onto the composite-metal junction. Based on the composite thickness and bolt cross-section researchers concluded that the ideal pressure distribution is achieved when using bolts with 19mm diameter. Another conclusion was that there is no significant difference of pressure distribution when using a protruding-head bolts vs. tapered-head bolts.
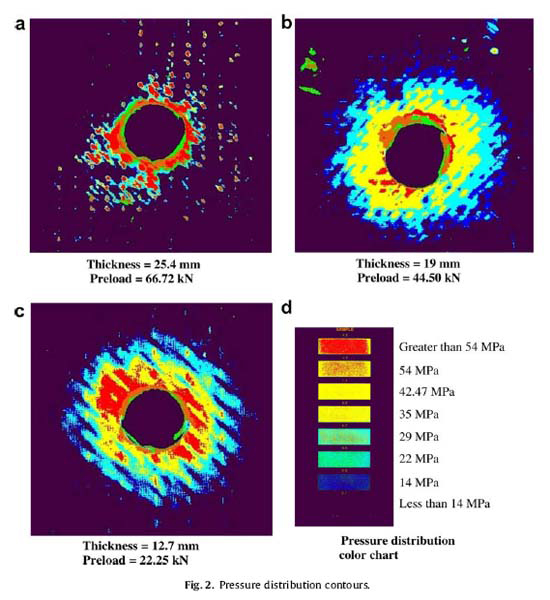
Based on this finding, engineers can calculate the needed tactile pressure to achieve a water-tight composite-metal bolted joint that can then be confirmed with a Fuji Prescale film, as shown below:
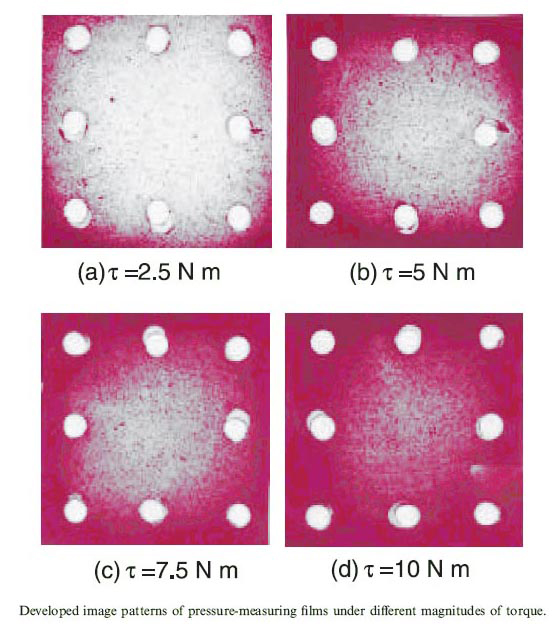
Thanks to the Fuji Prescale tactile pressure readouts, engineers can work toward finding the optimal number of bolts and bolt tightening force that will ensure minimal composite fatigue but still create a water-tight composite-metal joint.